

Submersible gates can be considered for thin-walled or small-part product designs, but such gates are not suitable for injection molding of parts with larger wall thicknesses, because such gates are more likely to occur in advance of the gate Freeze, thereby affecting the subsequent feeding effect of thick-walled products.ĥ) Good temperature control The fifth point is very important: good temperature control of the mold. The general injection gate design types are generally applicable to PEEK injection products. Depending on the PEEK grade you are molding, the minimum gate size is 1mm for unfilled PEEK and 2mm minimum for filled reinforced PEEK. At Victrex, there is a general rule that the gate is 2/3 the thickness of the maximum section thickness of the injection molded component. Use as large a gate design as possible to achieve better packing. Furthermore, higher processing temperature cooling gradients tend to result in greater shrinkage than lower temperature processing polymers. PEEK is a semi-crystalline polymer with higher shrinkage compared to amorphous thermoplastics. Gate size depends on part maximum wall thickness, number of cavities and part geometry. Fourth point: The large gate design is suitable for PEEK injection molding. Remember: any contamination that is inadvertently involved in the entire injection molding process can cause black spots in the final PEEK injection molded part.Ĥ) The product should use large-sized gate design as much as possible. Return material may be the main source of contamination, we recommend that you use special equipment and do its cleaning well to ensure that PEEK material is not contaminated by other materials during its operation.
#PEEK PLASTIC INJECTION MOLDING FREE#
Before starting injection molding of PEEK, it is important to clean the screw and barrel properly and efficiently to ensure that the equipment is clean and free of other material residues. As you will learn, most other polymers degrade at the processing temperatures of PEEK, necessitating the use of a clean oven and feed system. The third point is an important requirement: keep it clean! Avoid any contamination when handling PEEK. A dehumidifier or hot air dryer can also be used and must be able to maintain a dew point or saturation temperature of -40☌.
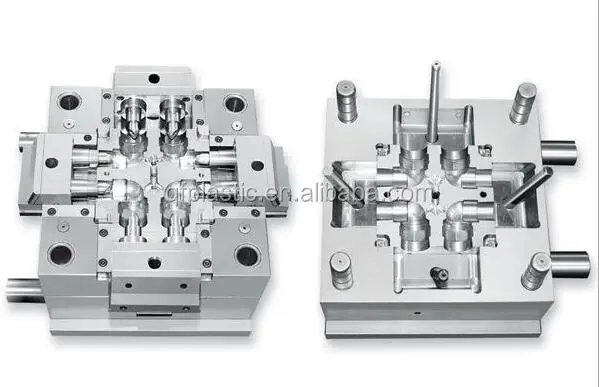
The aim is/should be to reduce the residual moisture content to <0.02%. In short, we recommend placing the pellets on the tray in a conventional oven and drying at 150-160☌ for 2-3 hours, optionally continuous drying. In our data sheet and injection molding guide, we provide some dry guidance. The second point pertains to dry PEEK polymers: PEEK pellets should generally be dry, but absorb moisture from the atmosphere. All metal parts should be smooth and highly polished to well avoid material degradation due to prolonged local residence in the barrel. Copper and copper alloy materials (in contact with the melt) should be avoided. Universal screw suitable for PEEK injection molding. In addition, the use of high-temperature-resistant insulation materials to insulate the barrel can also be considered, thereby saving energy costs. We recommend that you use a ceramic heating coil because of its higher heating consistency. If necessary, if a heating system modification is required, it is usually necessary to modify the heating coil or thermocouple/controller of the injection molding system. Most standard injection molding machines can reach these temperatures without retooling. PEEK grades, the processing temperature of the injection molding machine barrel will be between 350-400⁰C. The first is equipment for PEEK injection molding: PEEK can be molded on standard injection molding machines from most well-known machine suppliers. Five factors to consider in PEEK injection moldingġ) Equipment: Standard injection molding machine
